Before taking a closer look at the laboratory’s work, it is worth remembering that
metrology is the science specifying the methods for correct performance of measurement and is an integral part of Istituto Giordano’s history.
Indeed, right from the start, tests performed in Istituto Giordano laboratories have guaranteed the
metrological reliability of measurements with traceability to national standards and the International System of Units (SI).
To understand this sector’s importance, let us try to give a clearer description of 2 concepts:
Measurement traceability <--------------------------------------------------> Uncertainty of measurement.
Any measurement without associated uncertainty cannot be utilised; for example, if stating that the air temperature is 20 °C, but not specifying the reliability of this figure, no certainty exists; indeed, it could be (20 ± 1) °C or (20 ± 10) °C. In the latter case, knowing that today the temperature ranges from 10 °C to 30 °C is probably of no use and interest to the recipient of this information, it is probably something that he or she already knows! Therefore, to be able to estimate the uncertainty to be associated to my measurement, it is necessary that the thermometer that gave me the reading of 20 °C is traceable to the international temperature scale by means of an unbroken chain of calibrations linking it to national temperature standards.
Following this introduction,
we interviewed Pierluigi Latte, Head of the Metrology Laboratory, in order to take an in-depth look at this department.
Q: The laboratory calibrates various types of instruments: can you tell us which?
The metrology laboratory can perform calibration of a vast range of measuring instruments, such as thermometers, scales, pressure gauges, calliper gauges and torque wrenches, as well as work instruments and more accurate laboratory instruments. We also carry out a lot of on-site calibration where instruments cannot be moved, like for example, temperature sensors fitted to production-line machinery.
Q: Can you give us some specific examples of the calibration you perform?
The most interesting jobs are those carried out at customer premises where we come into contact with highly-specialised companies in often very different sectors. These include curing chambers for Langhirano ham, manufacturers of carbon parts for racing cars and motorcycles and, of course, producers of our famous Piadina Romagnola IGP flatbread where the regulations specify the hotplate temperature.
Q: On the basis of which authorisations/notifications is calibration performed?
Our metrology laboratories
are Accredia-accredited to ISO 17025 for the
temperature measurement sector and
direct current and low-frequency measurements. This accreditation confirms the competence of our metrology laboratories to produce measurements that can be traced back to the requirements specified by the General Conference on Weights and Measures.
Often, customers implementing a quality management system carry out calibration of their instruments in compliance with standard ISO 9001:2015, clause 7.1.5, particularly in the manufacturing and agrifood sectors.
Q: Let us go into more detail, which instruments do you use?
Normally, calibration of an instrument is performed by comparing the measurements of the instrument to be checked with our standards. To do this, the quantity to be measured needs to be reproduced in the laboratory in a steady manner. For example, to calibrate a thermometer capable of measuring 1000 °C, we have a furnace that reaches and maintains this temperature with a tolerance of a few tenths of a degree.
Q: What are the development times for a calibration?
Planning a new calibration calls for extensive preparation. Even before specifying the standards and equipment to be used, we must acquire full details of the physical principles upon which the operation of the instrument requiring calibration is based. This enables proper assessment of all influencing factors that are then used when estimating measurement uncertainty.
On the other hand, calibration at customer premises is a procedure that needs to be carried out as quickly as possible; therefore, following completion of the initial development and design stage, we aim to reduce timescales by standardising and, where possible, automating these activities.
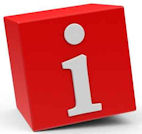
For more details
see the page.