Il pantografo
Il pantografo è una presa di corrente che consente, sui veicoli ferroviari, la captazione dell' energia elettrica da una linea aerea soprastante (catenaria) allo scopo di alimentare le apparecchiature come i motori, il riscaldamento elettrico, il condizionamento e tutti gli eventuali dispositivi ausiliari di bordo. E’ la più adatta ai mezzi di trazione per le potenze e le velocità elevate che si richiedono.
In generale, il pantografo è costituito da un sistema articolato (quadro mobile), montato sul telaio di base, ed installato a mezzo di isolatori sull’imperiale del rotabile. Il quadro mobile sostiene la testa di captazione munita di striscianti che sono a diretto contatto con il filo o i fili della catenaria.
Il sistema articolato consente all'archetto di spostarsi liberamente nel piano verticale senza perdere il contatto con la linea aerea. Gli striscianti sono costituiti da barre di materiale conduttore (rame, acciaio, alluminio, carbone) e sono la vera e propria presa di corrente in quanto a diretto contatto con i fili della linea aerea. I materiali con i quali essi sono costruiti sono tali da consentire una usura minima della linea.
Il pantografo, la cui altezza di lavoro può anche raggiungere 3 metri di altezza, è sollevato con dispositivi ad aria compressa e tenuto alla pressione stabilita, contro il filo della linea aerea, a mezzo di molle opportunamente tarate oppure, come in dispositivi più moderni a spinta impressa, da un azionamento pneumatico che adegua il valore della spinta in funzione della velocità di marcia a tutto vantaggio della qualità di captazione.
Descrizione del campione e scopo della prova
Il campione sottoposto a prova è costituito da un pantografo ferroviario, completo di tutti i componenti elettrici e meccanici, totalmente assemblato e installato sulla struttura di supporto utilizzata in servizio.
Lo scopo della prova è la verifica del comportamento a fatica delle saldature del braccio superiore, nonché il rilievo di qualsiasi altro fenomeno causato da fatica durante la prova stessa.
Allestimento della prova
Apparecchiatura di prova | Dettaglio dei sistemi di controllo delle pressioni |
 | 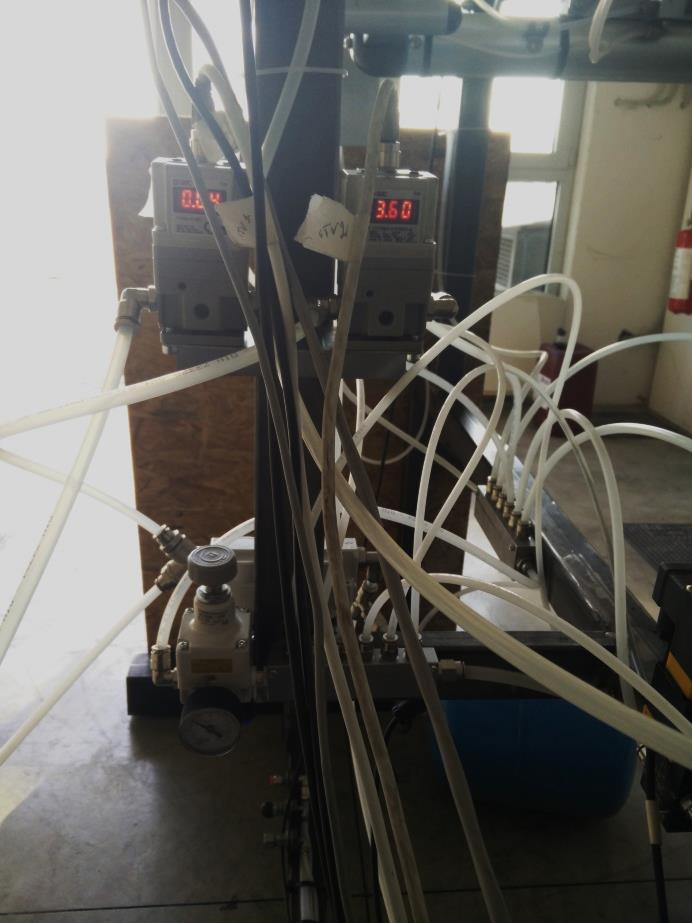 |
Dettaglio di fissaggi di sensori e attuatori |
Dal momento che il sistema di innalzamento originale del pantografo controlla la forza ma non la posizione è stato realizzato un telaio di supporto che sostenesse il campione nella configurazione di lavoro più critica.
Sul braccetto di sostegno degli striscianti sono stati collegati 6 pistoni pneumatici allo scopo di simulare le forze inerziali generate dal movimento del treno.
Un settimo pistone, simulante il carico prodotto dal contatto con il cavo, è stato posizionato sullo stesso braccio, distanziato 400 mm dal centro, per riprodurre la posizione di contatto più sfavorevole.
In prossimità dei punti di azione dei pistoni sono stati posizionati dei sensori di spostamento per misurare l’ampiezza delle oscillazioni e rilevare eventuali deformazioni causate dai carichi. Tutti gli attuatori e tutti i sensori sono stati collegati ad un PLC comandato da un programma sviluppato internamente. I dati in lettura sono stati inviati anche ad un PC per il monitoraggio in tempo reale e la registrazione. Anche qui è stata utilizzata un’interfaccia sviluppata internamente.
Esecuzione della prova
La prova è stata eseguita secondo le prescrizioni concordate con il cliente e si è sviluppata secondo le seguenti fasi principali:
- Test preliminare statico di applicazione dei singoli carichi; misura delle deformazioni e delle sollecitazioni per ogni singolo carico;
- Applicazione simultanea dei carichi di fatica. I carichi sono stati applicati a frequenza di circa 2 Hz, Le coppie di pistoni lavoravano a frequenze leggermente diverse per poter coprire tutte le combinazioni di carico possibili. Sospensione della prova di fatica ogni 2.0 milioni di cicli per effettuare le attività di misura delle deformazioni e il controllo visivo del pantografo per verificare la presenza di eventuali danni;
- Al termine della prova è stato effettuato un accurato controllo visivo di tutti i componenti del pantografo ed in particolare dell’upper arm, per il rilevamento di possibili danni o rotture.
Durante la prova non è mai stato rilevato alcun segno di rottura o cedimento né delle saldature sotto esame né di alcun altro componente del campione.
Si ringrazia il committente
Production Group Srl per l’autorizzazione alla pubblicazione dei contenuti descrittivi e fotografici.
Per visualizzare tutte le nostre attività in ambito ferroviario, consulta anche la pagina dedicata "Prove di laboratorio settore ferroviario"